On September 10, 1997, the Mirror Lab personnel opened the furnace to reveal a very beautiful looking 8.4-m honeycomb mirror! This casting was the world's largest optical telescope mirror blank made from a single piece of glass (a title now held by LBT #2).
Casting of the mirror took place in mid-January 1997. Subsequently, the mirror underwent an eleven week annealing and cooling process, followed by inspection early April. After extensive analysis, it was confirmed that the leakage of glass noted during the casting resulted in some thinning of the mirror's faceplate. An area amounting to approximately 10% of the total surface of the mirror was of less than optimum thickness. Apparently the hydrostatic forces from the liquid glass caused several of the tub wall segments to shift and open the joints to allow glass leakage. Two tons of glass were added to the mold in late April and a slow heating process was started. The highest temperature for flash melting of the new glass occurred on June 10. After a cool down period of three months, the mirror was ready for inspection again. This time the news was good: the face plate had been found to be uniform with an average thickness of 1.65 inches . There were very few small bubbles, the majority of which will be removed during the generating and polishing process.
The furnace wall sections and the Inconel bands that encircle the mold were removed. On February 23, 1998 the mirror was lifted into a vertical orientation and positioned in the cleaning station where the ceramic refractory material was removed using high pressure water jets.
By July 24, 1998 all of the mold material had been removed from the inside of the glass honeycomb. The the 8.4-m mirror had to wait a few months for completion of polishing on the Magellan 6.5-m mirror.
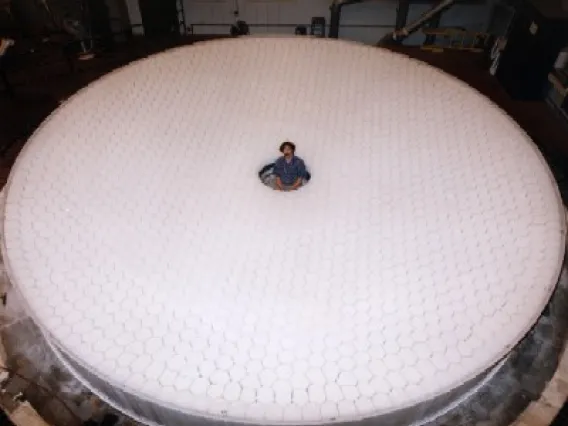
To get some idea of the size scale of the mirrors we construct, note the optician in the central hole (Picture to the left) of the 8.4-m primary mirror for LBT. He is about 6 ft 6 in tall ( ~ 2 m). The hexagonal (honeycomb) structure of the mirror can be seen through the front surface of the glass. There are some 1728 cores or columns that go into creating the light weight structure of the mirror.
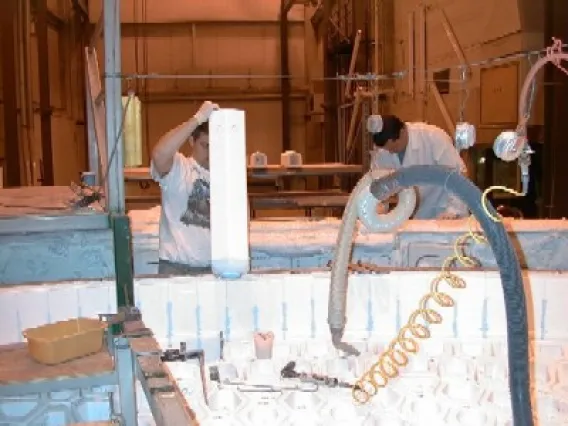
Randy Lutz and John Martin (Right) are installing hexagonal cores on the floor of the oven that become the honeycomb structure within the mirror. The cores are made of alumina silica that remain rigid while the glass is liquid at temperatures of ~1160 C. Each core is held in place with a silicon carbide bolt.