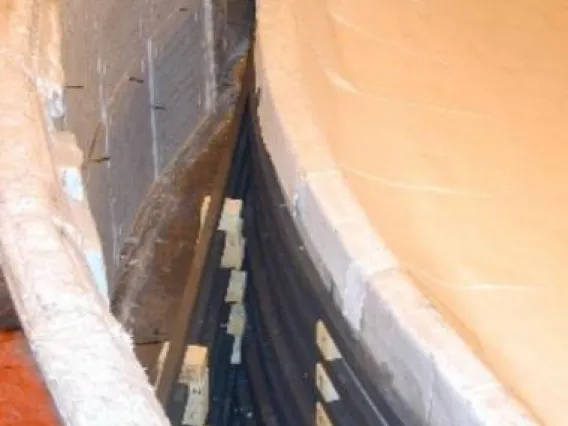
This is a view of the outer edge of the LBT2 mold (Right). Some of the 124 inconel bands are seen wrapped around the silicon carbide tub walls. The inconel bands stabilize the tub walls against the hydrostatic pressure of the molten glass once it has melted and filled the mold. Each of the inconel bands has a pneumatic cylinder attach to each end that pulls on the band with about 600 pounds of force.
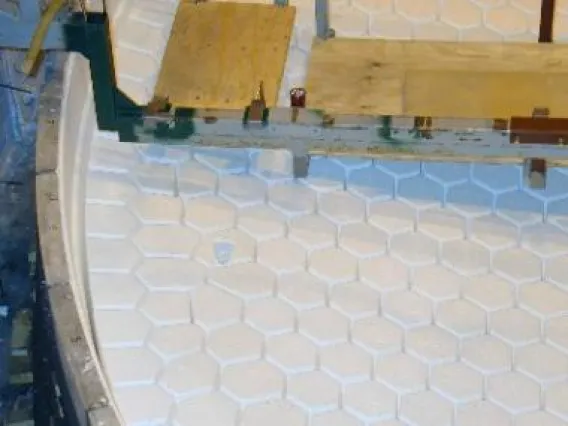
Top view of a portion of the 1662 cores that are used to form the honeycomb mold for the LBT2 mirror blank. The cores are made of an alumina-silica refractory that can withstand the 1150 degree Celsius casting temperature. Most of the cores are hexagonal shaped, however the outer three rows are a combination of shapes used to adjust from the hexagonal pattern to the circular perimeter of the mold.
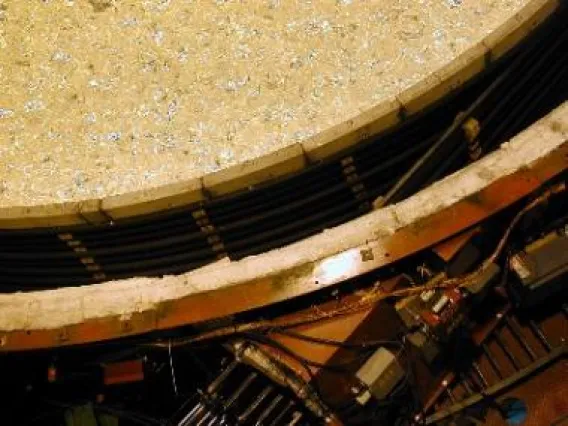
All the glass has been loaded into the LBT2 mold and it is ready for casting. The E6 borosilicate glass is supplied by Ohara Corp. The glass arrives in chunks that vary in size from 1 to 15 pounds. Each chunk is systematically inspected to insure that any inferior glass is removed prior to hand placement into the mold. 40,987 pounds of glass were used to cast the LBT2 mirror blank.
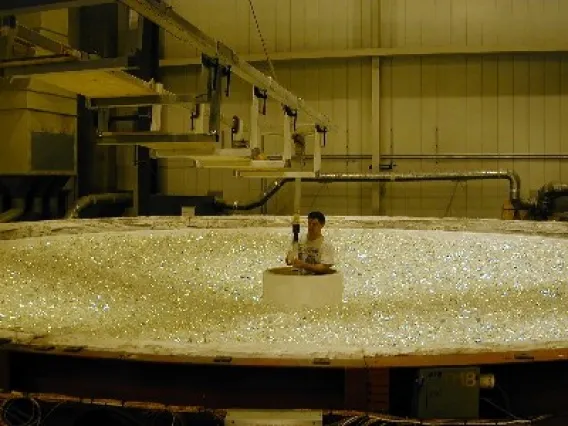
This gives a reference scale to the size of the LBT2 mirror blank. The platform used by the staff to load the glass into the mold is being removed prior to installing the lid to the furnace.
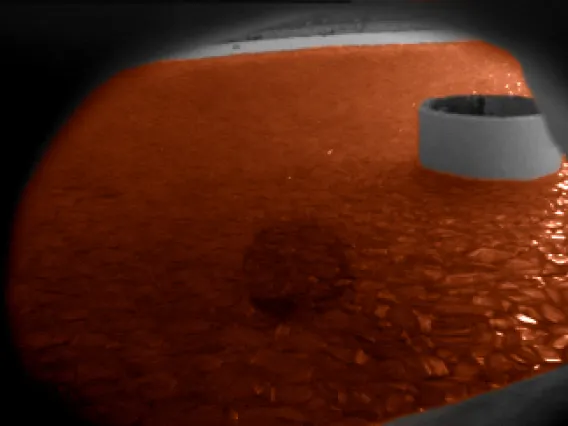
The furnace used to cast the LBT2 mirror blank has an array of 7 cameras that peer into the furnace to monitor the progress of the casting. From one of the cameras you see the glass at a temperature of about 900 degrees Celsius. It has softened enough to settle into a somewhat uniform 6" thick mass but is still solid enough for the original shapes of the glass chunks to be seen. At this temperature the furnace is rotating at a speed of 6.73 RPM's. Upon further heating, the glass will flow down the space between the cores to form the honeycomb mirror.